事例紹介
企業概要
業種 | 食品原料メーカー |
---|---|
売上規模 | 約80億円 |
代表者 | 製造畑(60代) |
原価整備 | 材料費中心 |
---|---|
悩み | 材料費高騰 価格設定 予算の作り方 |
社長 (製造畑:60代)
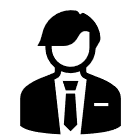
- どの商品が儲かっていて、どの商品が損しているのかが明確になった
- 製造もどこがダメなのか分かり、打手が明確になった
- これまでなかなかのんでもらえなかったが、値上げを根拠を示してのんでもらえた
生産管理 (課長)
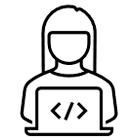
- 製造・営業の会議でしっかりと根拠を持って伝えられて、一緒に改善に取り組めるようになった
- ベースとなる製品を利用することで、新製品の原価を簡単に算出することができるようになった
取り組み内容
- 製品別原価の算定(売上95%をカバー)
- 製品別利益の可視化
- 歩留まり情報の可視化
- レシピや製造ロット変更によるシミュレーション
- 予算策定と製品別目標設定
成果
- 製品売価の値上げ実現(顧客との交渉)
- 製法変更・ロット変更による赤字製品の減少
- 必要な投資の見直し(歩留まり改善に注力)
- 経営(管理)・製造部・営業部の連携促進
- 社内データ整備による管理の負担軽減
事例2
企業概要
業種 | 部品製造 |
---|---|
売上規模 | 約15億円 |
代表者 | 営業畑(40代) |
原価整備 | 過去の経験則 |
---|---|
悩み | 営業赤字 高い不良率 慢性的な残業 |
社長 (営業畑:40代)
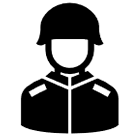
- OEM先から言われた原価がうちの実情と合ってない部分があることがわかった
- 原価を整備して、極小ロットの生産を止めてから利益が増えてきた
- 見積もりの基準ができたことで営業が自信を持って仕事をとれるようになった
製造 (部長)
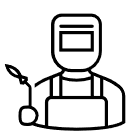
- 設定した原価に対して、自分たちの活動の結果、どうコスト削減できたかが明らかにできてうれしい
- 設定した工数で、今後の予定工数が分かるようになった。活用を進めていけば、更に人件費が抑制できそう
取り組み内容
- 製品別原価の算定(売上90%をカバー)
- 製品別利益の可視化
- 歩留まり情報の可視化
- 原価計算結果に基づく製造改善策策定
- 予算策定と製品別目標設定
成果
- 半期での黒字化(前期は営業損失数千万円)
- 不採算の原因となる極小ロットの製品の廃盤
- 主要カテゴリーの良品率の改善
- 変動人件費の削減
※一方で賞与はアップ - 営業見積もり精度アップによる赤字案件の撲滅
主な導入実績
No | 業種 | 売上規模 | 従業員数※ | 工程数 | 工場数 | 製品数 |
---|---|---|---|---|---|---|
1 | 食品加工 | 約10億円 | 約80名 | 20工程 | 2工場 | 約150 |
2 | 製菓製造 | 約3億円 | 約30名 | 23工程 | 1工場 | 約300 |
3 | 水産加工 | 約10億円 | 約60名 | 16工程 | 1工場 | 約60 |
4 | 食肉加工 | 約5億円 | 約50名 | 22工程 | 1工場 | 約700 |
5 | 食品原料 メーカー |
約80億円 | 約200名 | 100工程 | 2工場 | 約500 |
6 | 自動車部品 | 約15億円 | 約100名 | 35工程 | 3工場 | 約300 |
7 | 電子部品製造 | 約20億円 | 約70名 | 18工程 | 2工場 | 約250 |
8 | 金属部品製造 | 約15億円 | 約90名 | 21工程 | 2工場 | 約1,200 |
9 | 建築資材 | 約30億円 | 約50名 | 23工程 | 3工場 | 約300 |
10 | 素材メーカー | 約40億円 | 約60名 | 28工程 | 2工場 | 約150 |
※パート・外国人労働者も含む